Drilling machines, essential in the realms of construction, mining, and numerous industrial processes, embody technological advancement and human ingenuity. These machines, designed for boring holes into various materials, come in a multitude of types, each tailored for specific tasks and applications. This article delves into the world of common drilling machines, exploring their types, functions, and the industries where they are pivotal.
The Versatility of Auger Drills
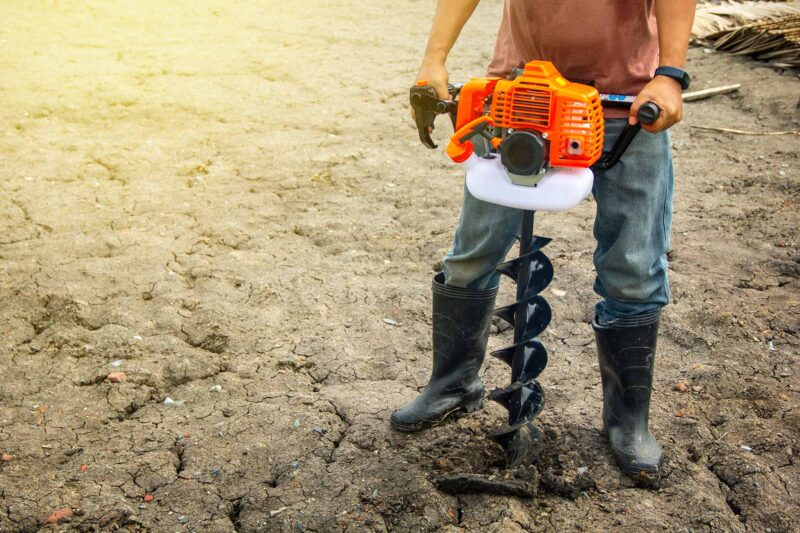
Among the most familiar drilling machines are auger drills. Characterized by their helical screw blade, often termed a ‘flighting’, augers are used for making holes in the ground or materials like wood. In construction and geotechnical engineering, they are instrumental for tasks such as soil sampling and to create foundations. Their simplicity makes them adaptable for both hand-held and larger, mechanized versions. Learn more on auger drills at Sigma Plant Finder.
Hand-Held Electric Drills: A Toolbox Staple
On a smaller scale, hand-held electric drills are ubiquitous in both professional and domestic environments. These compact devices, fitted with various drill bits, are capable of piercing through wood, metal, plastic, and masonry. With features like variable speeds and reversible functions, they offer precision and control, making them indispensable for a range of tasks from simple home repairs to intricate manufacturing processes.
The Power of Radial Arm Drills
Radial arm drills are recognized for their large size and power. These stationary machines feature a radial arm, allowing the drill head to be positioned over the workpiece. This design provides flexibility and reach, making them ideal for heavy-duty tasks in fabrication shops and large-scale construction projects where large and heavy workpieces require drilling.
The Precision of Milling Machines
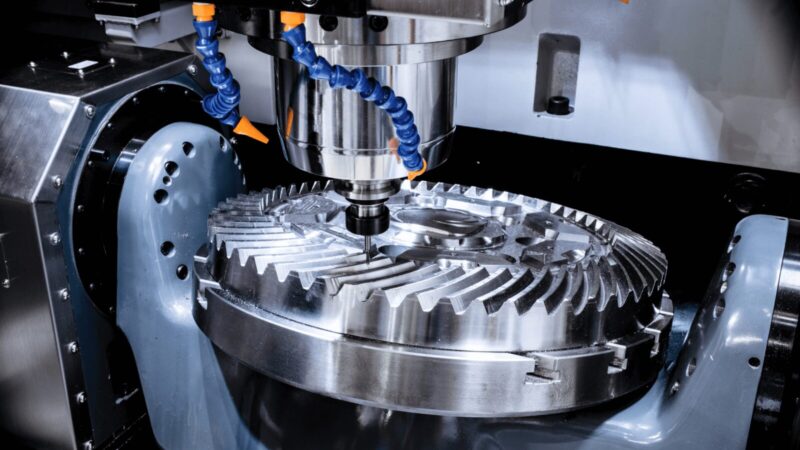
Milling machines, though primarily used for cutting and shaping metals, also incorporate drilling capabilities. These versatile machines use rotary cutters to remove material, allowing for operations ranging from simple drilling to complex shaping and surface finishing. Their precision and ability to handle complex tasks make them invaluable in machine shops and manufacturing industries.
Bench Drills: The Workshop Workhorse
Bench drills, or drill presses, are smaller than radial arm drills but offer more precision than hand-held drills. Mounted on a bench, these machines can drill accurate and consistent holes in various materials. They are a staple in workshops and are favored for tasks that require repeated drilling with uniform depth and size.
The Robustness of Magnetic Drills
Magnetic drills, or mag drills, are a specialized type that utilizes a magnetic base to adhere to metal surfaces. This feature allows for drilling in horizontal, vertical, or overhead positions. Common in steel construction and heavy metal fabrication, mag drills are prized for their portability and ability to drill into hard metal workpieces with precision.
The Impact of Hammer Drills
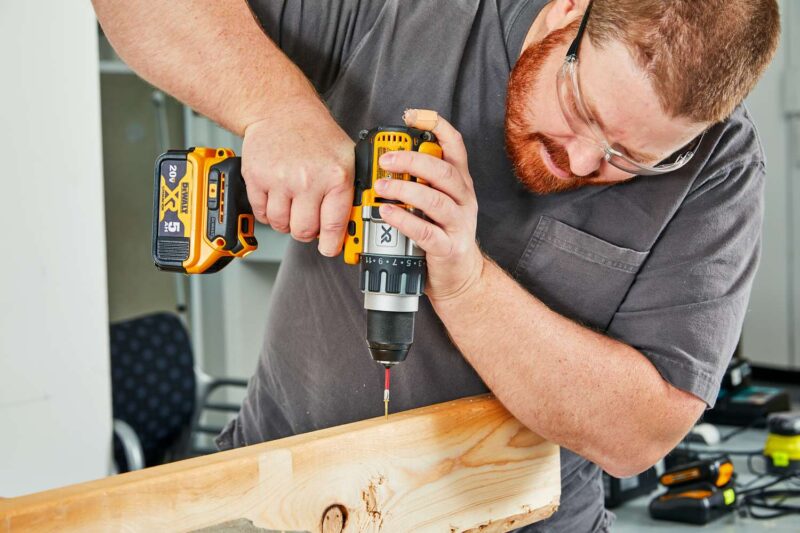
Hammer drills bring an added functionality to the conventional drilling mechanism. They combine rotation with a hammering action, enabling them to bore into hard materials like concrete and stone. This dual action makes them particularly effective for construction and masonry work, where they are used to create holes for anchors, bolts, and conduits.
Core Drills for Material Sampling
Core drills are specialized for taking samples of materials, particularly in geology and construction. These drills remove a cylindrical core from the drilled material, providing a sample for analysis or testing. Core drills are used in mineral exploration, concrete testing, and even ice-core sampling in polar research.
The Specialized World of Deep Hole Drills
Deep hole drilling machines are designed to produce deep, accurate holes in metal workpieces. They are used in applications where depth-to-diameter ratios are extreme, such as in the aerospace, oil, and gas industries. These machines often employ specialized techniques like gun drilling or BTA drilling to achieve the required depth and precision.
Exploring the Dynamics of Directional Drilling
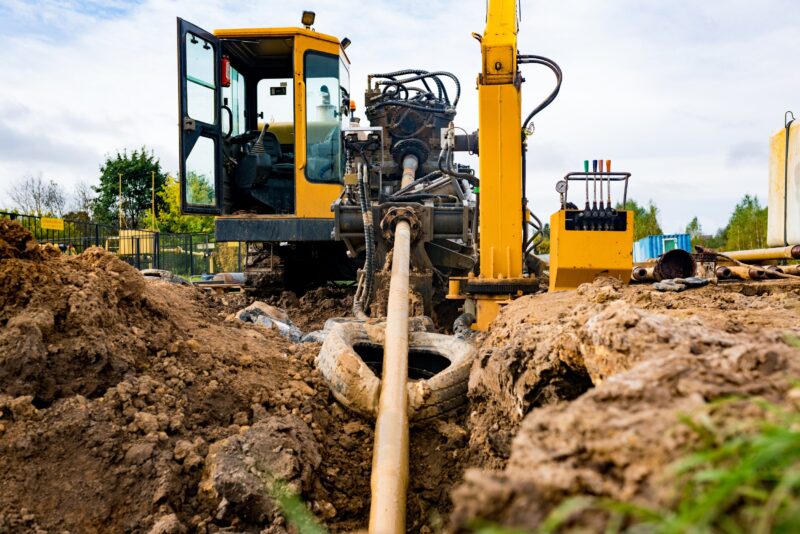
Directional drilling, a refined method distinct from traditional vertical drilling, offers enhanced control over the direction and angle of the drilled hole. This technique is pivotal in the oil and gas industry, allowing for the drilling of wells at various angles, maximizing access to resources while minimizing environmental impact. The technology behind directional drilling is complex, involving advanced monitoring systems and flexible drill pipes, making it possible to navigate around obstacles and reach targets that are not vertically accessible from the drilling site.
Understanding the Role of Rotary Drills in Heavy-Duty Operations
Rotary drills, often seen in mining and quarry operations, are designed for penetrating through hard rock and other tough materials. These large, powerful machines use a rotating drill bit, typically tipped with diamonds or hardened metals, to grind away at the material. The process involves the use of a drilling fluid, which cools the drill bit and removes the drilled material from the hole. Rotary drills are essential in creating blast holes in open-pit mining and are also used in large-scale construction projects for foundation work.
Advancements in Automated Drilling Technology
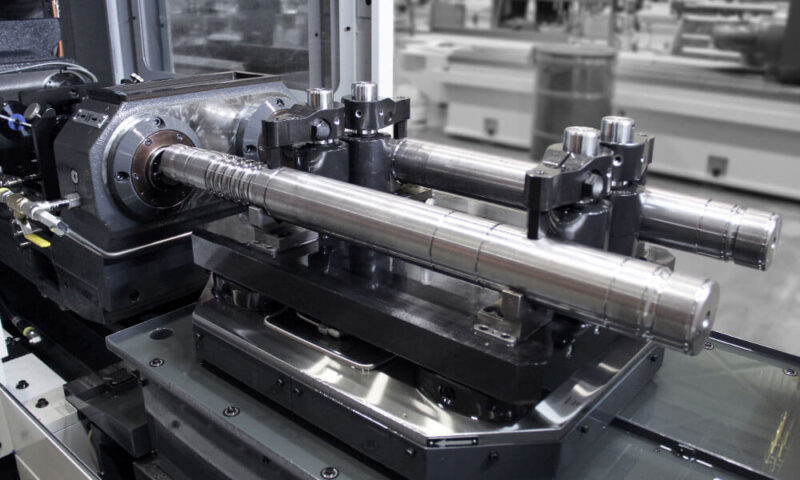
The evolution of drilling technology has seen a significant shift towards automation. Automated drilling machines are increasingly being used in various industries to enhance precision, safety, and efficiency. These machines are equipped with computer-controlled systems that allow for precise control over drilling speed, depth, and angle. Automation in drilling not only improves accuracy but also reduces the risk of accidents and human error, particularly in hazardous or challenging environments.
Summary
In conclusion, the world of drilling machines is as diverse as it is essential. Each type of drill serves a unique purpose, from the common hand-held electric drill to the specialized deep hole drill. These machines are fundamental to various industries, enabling us to accomplish tasks that range from simple home repairs to complex industrial manufacturing. Understanding the different types of drilling machines and their applications is key to selecting the right tool for the job, ensuring efficiency, precision, and safety in any drilling task.
Related Posts:
- Exploring Narcissistic Patterns: How They Treat…
- Understanding the Common Criminal Offenses and the…
- Strategic Access Management: Exploring Common Use…
- 9 Best Sci-Fi Movies of 2015: A Journey Through…
- Best Sci-Fi Movie Marvels of 2016: A Journey Through…
- Femitheist Advocates Society of Sameness and Almost No Men